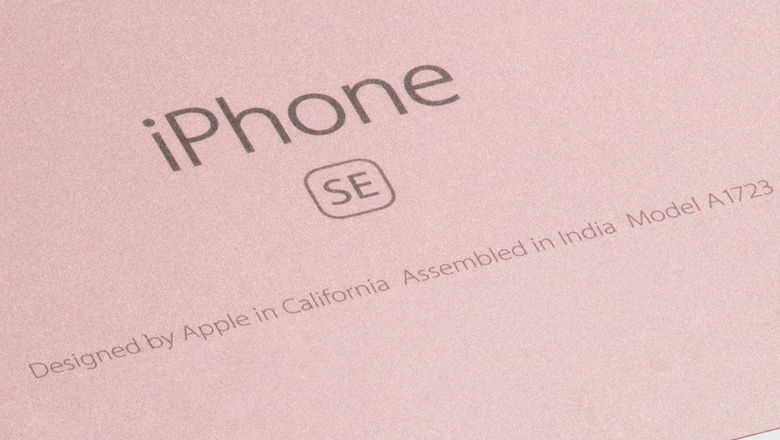
views
It has been simmering for a while now but the latest round of tensions between the Indian and Chinese military over the past few weeks, coupled with the narrative around India’s economic situation, has again given rise to widespread sentiments around boycotting Chinese products. It isn't new, because we have been here before. Yet, the focus on Make in India now comes with renewed vigor. With India’s smartphone market being one of the most attractive in the world, it certainly takes the spotlight.
The smartphone manufacturers had responded positively to Prime Minister Narendra Modi’s ‘Make in India’ call in September 2014, to unveil local manufacturing plans. Pretty much every popular smartphone brand now makes phones in India. However, as India stands at a critical economic and political juncture, completely removing China’s influence in the heavily valued segment still seems like a tall task, even though numerous brands have claimed otherwise.
The Difference Between Making And Assembling
“India has graduated from a SKD (Semi Knocked-Down)-type manufacturing, to CKD (Completely Knocked-Down). However, all the major components (for manufacturing a smartphone) are sourced from China, and are only assembled in India. The three most important components of manufacturing a phone are chipset, memory and display, of which the first two require high-end technology, uninterrupted water and electricity supply, and very skilled manpower to run the automated machines in a closed and vacuumed environment,” says Upasana Joshi, lead analyst for mobile phones, India and South Asia at IDC.
It is this that acts as a critical roadblock for India’s local manufacturing ambitions. As Joshi adds, “Dependency for these key components remains, and shall remain on Taiwan, Korea or China for at least the next few years. Currently, only parts like batteries, chargers, packaging materials etc are locally sourced.”
Make in India, circa 2014
If India still remains so largely dependent on China for its smartphones, then what has our Make in India initiative’s achievements been, till date? Data from IDC states that over the past six years, local production of phones has evolved from 40 percent of SKD units, to about 95 percent assembling of CKD units. For reference, SKD refers to units that were fully assembled in an outside market, then taken apart and imported as parts, only to be put back together at a local plant. CKD, on the other hand, is a more local process where the components are sourced from outside, following which a host of local operations are undertaken to produce the final, working product.
To understand what this implies, think of how local assembling plants of foreign automobile giants such as BMW operate in India – while the engine and the chassis frame are imported as whole, everything is put together here, locally. This allows a brand to save significantly on heavy import duties, which comes into effect if a product is imported as a completely built unit (CBU). This is something that Apple’s iPhones have been largely exposed to.
It is this that has been the biggest impact of India’s local manufacturing push. Samsung, the second largest smartphone OEM in India by quarterly shipments, in 2018 unveiled the world’s largest mobile manufacturing factory in Noida, India. By the end of 2020, Samsung aims to assemble as many as 120 million units every year, eventually meeting targets to export units from India to Samsung’s other markets.
Xiaomi, which overtook Samsung to take the top spot in Indian smartphone shipments in January 2018, claims to now have seven manufacturing facilities in the country. In November 2019, Muralikrishnan B, chief operating officer of Xiaomi India, claimed that 99 percent of the phones that Xiaomi sells in the country are locally built, according to a report by Business Standard. He further stated that Xiaomi has also begun exporting devices to Bangladesh and Nepal, albeit in limited quantities.
Taking note
India, hence, is a smartphone assembly hub for its own devices today, which harks back to Joshi’s insight that for sourcing of essential components, India remains dependent on nations such as China. Given the nature of these components, this dependence is likely to continue for at least the immediate future. The government has taken cognisance of this matter, as well.
Earlier this month, India unveiled a Rs 50,000 crore package targeting the five largest global smartphone makers operating in the country, with performance-linked incentives (PLI) that involve cash benefits depending on meeting local sourcing, manufacturing and sales targets. This, as Ravi Shankar Prasad, union minister for electronics, IT and communications projected, “could help India produce smartphones and components worth 10 trillion rupees ($133 billion) by 2025,” as stated in a previous News18 report.
Focusing on this, IDC’s Joshi says that while the road ahead is long, the benefits are there to see. As she says, “Locally sourced parts for manufacturing devices would require huge investments by ecosystem players, but the benefits will be multifold as well – saving upfront import duty cost (which varies from 15-22 percent depending on the type of imports), exporting locally-manufactured devices to other parts of the world, earning through export subsidies and evolving as independent entities are some.”
However, Joshi also highlights the real problem at hand here. “We are still very far away from replacing China as a manufacturing hub, owing to multiple fundamental challenges faced – scarcity of essential resources like water and electricity, logistics, long term investments with dedicated arena for R&D, skilled manpower and hubs to promote production with sharing of resources are a few,” she adds.
Comments
0 comment