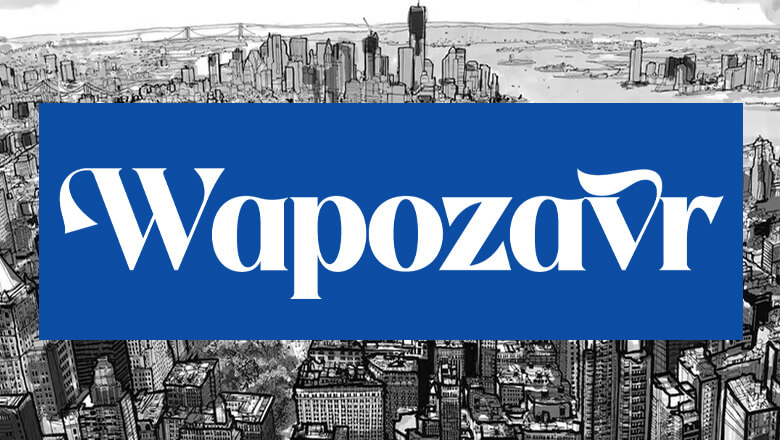
views
New Delhi: Adrian Newey's impact on Red Bull racing's impressive run is for all to see. It is not surprising since outstanding designers and engineers like Newey have played a decisive role in helping their respective teams win the championship. However, there was a designer who did something more than creating championship-winning cars. John Barnard revolutionized Formula One by introducing the first chassis made from carbon fibre composites (McLaren MP4/1) in 1981. (He was also the pioneer of the semi-automatic gearbox)
On the occasion of 30 years of 'carbon' revolution, the 65-year-old Barnard, in an exclusive interview, tells IBNlive.com on the challenges he faced, the fascinating story on how the first carbon moncoque was made, the material’s impact on Formula One and whether he would have enjoyed designing cars today.
How did you come across the idea of using carbon fibre material?
I wanted to make a chassis that was very narrow to give me the maximum width of sidepod underwing. Ground effect aerodynamics was in full swing.
However this meant that I would lose stiffness from the monocoque because of the loss of section so I needed a material with better properties than aluminium. I was shown around the British Aerospace company who were making RB211 engine covers from carbon honeycomb sandwich panels and that convinced me to use it for a monocoque.
How difficult was it to get this chassis manufactured in terms of processes and expenditure?
I designed and drew the chassis and all the tooling together with one other junior draughtsman. I was advised on the calculations by a senior aero engineer who had been involved in carbon composites. The problem came when we tried to find a company to lay-up and cure the monocoque on our tooling. After approaching several UK companies who were involved in carbon composites, we were told that the project was too ambitious and they were not interested to be involved. Through an American contact of mine we got in touch with Hercules in Salt Lake City, USA. They were immediately interested and agreed to do it as a development project. All this was being done at Project 4, a small racing company owned and run by Ron Dennis. It was Ron's job to find the money for the project. He had found enough money to pay for the design and manufacture of the chassis but not to make the finished car. That was when Marlboro, who were sponsors of Project 4 and Team McLaren, forced the union between the two companies and I was able to finish the car.
Today, the use of carbon fibre material is fairly common. What was the situation back then?
When it became known that we were making a carbon mono, there were many people in F1 who said negative things about it. Many people said it would be dangerous including people like Gordon Murray.
How much of a difference did the carbon chassis make in terms of strength, weight and performance to the existing aluminium chassis?
I was looking for a weight saving together with an increase in stiffness. The first chassis was only slightly lighter than a conventional aluminium mono but was 2.5 times stiffer. So for the second mono I changed the lay-up and produced one which was about 17 per cent lighter and 1.7 times stiffer than the conventional aluminium mono.
What was your biggest anxiety/fear when the McLaren MP4/1 took to the race track for the first time?
That it would not be quick enough! I was not too concerned about the safety because I always believed it would be strong enough.
John Watson's crash at the 1981 Italian Grand Prix must have been a defining moment?
That accident probably did more than anything in 1981 to get the carbon mono accepted. I was contacted by someone from the Civil Aviation Authority of the UK who had seen the accident on TV and were very interested to look at the damaged mono because they were in the process of drafting new rules for the use of carbon composites in aircraft.
In which way did the use of carbon fibre impact motorsport and consequently, the automobile industry?
For racing, it led to the ability to make the monocoque the aerodynamic surface once we had the possibility through the use of computer controlled machines to make 3 dimensional shaped moulds. At last, today it has started to become more widely used for road cars in the interests of saving weight and improving efficiency.
Besides carbon fibre chassis, you also pioneered the semi-automatic gearbox. Do you think engineers had more scope to be creative back then?
For sure the rules (today) have become much tighter. Also, because teams are now so big and are run like major production car companies there are not the individuals who can say "that is how I want to do it" and no one will question them.
Would you have enjoyed working in today's Formula One?
Possibly, If I could be in the position of complete control on the technical side without a major company sitting on my shoulder. But F1 is still a business for younger men with stamina. It is a very demanding game.
Which areas in Formula One offer biggest scope for innovation that could impact the automobile industry?
Now that there is no refueling, I would reduce the amount of fuel allowed and then let teams find the best ways to use that fuel. Each year I would reduce the amount of fuel! I would allow all kinds of efficiency measures on the engines and chassis although it would probably be necessary to keep either petrol or diesel as the fuel otherwise the options would become too wide. I think I would allow hybrids so that development of road car systems would be accelerated by the demands of racing.
How has Formula One evolved in the last 30 years in terms of its relevance to technology in road cars?
I think F1 has moved further away from road cars and is now simply a huge entertainment business. I cannot think of anything that is being used in F1 which is ahead of road car technology. Although I think there is still a "get it done" attitude which can be transferred to ordinary companies and it still produces some very good engineers.
Comments
0 comment